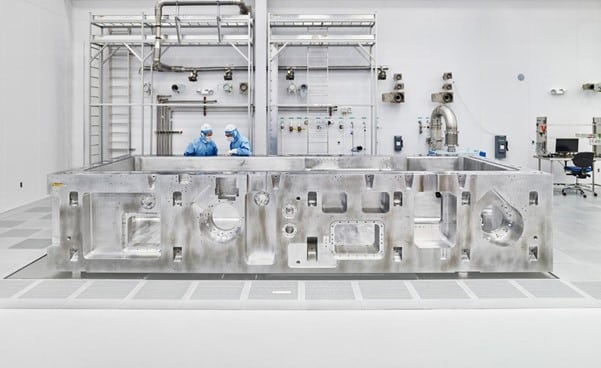
ASML 차세대 극자외선 장비의 상부 구조물은 알루미늄으로 이루어져 있으며, 그 무게는 17톤에 이른다. CHRISTOPHER PAYNE
Inside the machine that saved Moore’s Law
무어의 법칙을 실현시킨 일등공신
네덜란드 기업인 ASML은 더 높은 집적도의 반도체를 개발하기 위해 17년간 90억 달러(약 10조 7천억 원)를 투자했다.
패트릭 웰런(Patrick Whelan)은 클린룸(청정실) 방진복의 안면 덮개 너머로 일이 진행되는 모습을 살펴본다.
그의 앞에는 토스터 크기의 반짝이는 유리 조각이 있는데, 이 유리 조각은 무게를 줄이기 위해 파낸 부위가 커서 기묘한 토템처럼 보인다. 웰런의 팀은 그것을 커피 탁자 크기의 알루미늄 구조물에 붙이고 있다. 금속과 유리 모두 미세한 오차를 제거하기 위해 몇 주 동안 연마 과정을 거쳐 섬뜩할 정도로 매끄럽다. 앞으로 24시간, 접착제가 굳는 동안 작업자들은 유리와 금속이 서로 정확하게 결합하도록 신경을 곤두세워 관찰할 것이다.
웰런은 기구를 향해 손짓하며, “이것들은 마이크로미터 수준의 정밀도로 배치될 것이다.”라고 필자에게 말했다.
근처 기술자 한 명이 그가 너무 가깝다고 우려하며 소리쳤다. “물러서요!”
“안 만졌어요! 안 만졌어요!” 웰런이 웃으며 말했다.