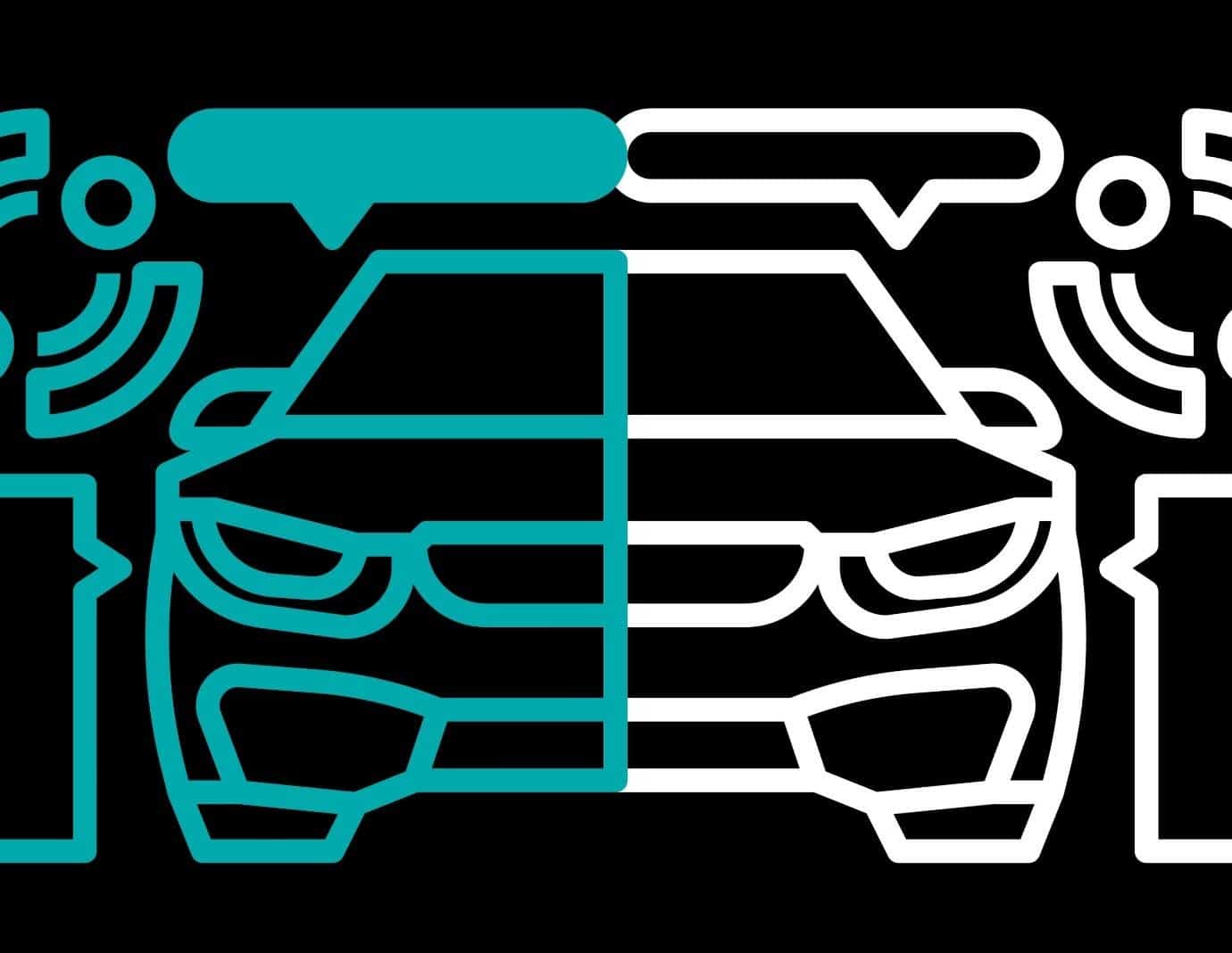
디지털 트윈이 실제 제조 과정을 개선해주고 있다.
Digital twins improve real-life manufacturing
컴퓨터로 열일하는 쌍둥이 ‘디지털 트윈’
컴퓨터 속에 가상의 ‘쌍둥이’를 만들어 다양한 상황을 시뮬레이션하는 방식을 ‘디지털 트윈’이라고 부른다. 이러한 디지털 트윈은 새로운 제품이나 서비스를 개발하는 복잡한 과정을 효율적으로 전환하는 데 도움을 주고, 제품의 다양한 측면을 이해할 수 있는 통찰을 제공한다.
미국 방산업체 레이시온 테크놀로지스가 2021년에 실시한 미사일 방어용 요격체 발사 시험은 계획대로 무사히 진행됐다. 레이시온이 이 시험과 관련한 전 과정을 시뮬레이션을 통해 사전에 테스트해본 게 도움이 됐다.
독일 IT 기업 지멘스와 미 항공우주국 나사의 제트추진연구소(Jet Propulsion Laboratory)는 방사성 동위원소 열 발전기로 움직인 화성 탐사 로버 큐리오시티(Curiosity)를 가지고 시뮬레이션하면서 발전기의 열 방산 문제 해결을 위한 공동 연구에 착수했다.
일본의 타이어 전문업체인 브리지스톤도 유럽에서 ‘킬로미터당 가격’ 서비스를 제공하기 위해 실제 차량에서 수집한 데이터를 적용해 타이어 성능을 시뮬레이션하고 있다.
지금 언급한 사례들처럼 컴퓨터에 현실 속 사물의 쌍둥이를 만들어 현실에서 발생할 수 있는 상황을 시뮬레이션해서 결과를 예측해보는 기술을 ‘디지털 트윈(digital twin)’이라고 한다.
레이시온의 ‘모델기반 디지털 스레드 프로세스 역량 센터(Model-Based Digital Thread Process Capability Center)’의 알베르토 페라리(Alberto Ferrari) 수석 책임자는 “회사가 제품의 프로토타입 생산을 시작하거나 현장에서 제품을 관리하기 전에 문제를 파악하고 해결하기 위해 디지털 트윈을 활용하고 있다”면서 “실제 데이터를 기반으로 하는 디지털 트윈을 이용하면, 의사결정에 실질적인 도움을 주는 모델을 파악할 수 있다”고 말했다.